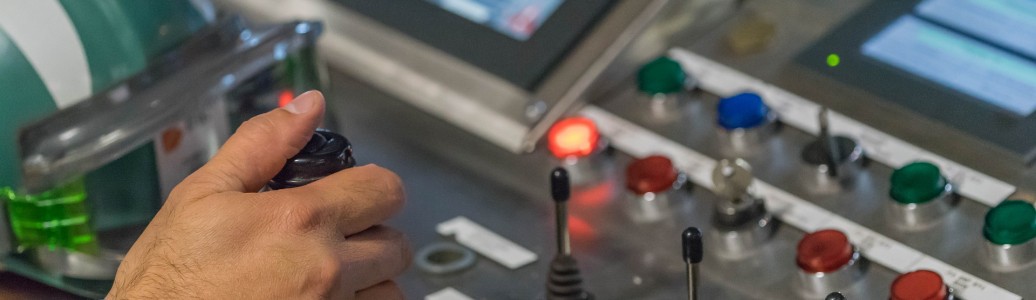
According to the International Federation of Robotics, worldwide robot installations now sit at a colossal 400,000 units per year – and this figure is set to surpass half a million by 2022. Considering buying a robot? You should. But not before determining three virtual calculations: ROI, payload and inertia. Nigel Smith, President and CEO of Toshiba Machine.
Return on investment (ROI)
To gain a clear ROI estimation, you must first calculate the predicted robot usage. Let’s say you plan to use two SCARA robots. The robots will run for three shifts a day, six days a week, 48 weeks of the year. The equivalent labor usually requires two operators per shift, equating to six operators to complete the same throughput over a working week.
Using the average salary of a production operative as an example, at £25,000 per annum, removing these roles would reduce labor costs by £150,000 a year. However, even with a robot, human labor is not entirely eliminated. A good rule-of-thumb for labor estimations alongside a robot is 25 per cent of current costs, reducing the total labor budget to £37,500 per year. Minus this figure from the total robot purchasing cost, and you have an estimated first year ROI.
Naturally, there are some flaws in this calculation. This process does not consider problems, such as breakdowns or unplanned downtime. For a more accurate reflection of ROI, conduct a cost analysis based on the operations of the facility, as well as a risk assessment.
Payload and EOAT
Robot payload describes the weight a robot arm can lift. Determining the required payload in advance of purchase is essential. Let’s face it, installing a robot that cannot lift your goods could be a colossal waste of expenditure.
The maximum payload that a robot manufacturer states in the product’s datasheet should usually include the weight of the end of arm tooling (EOAT) — that’s the robot gripper, welding torch, sensor, soldering tool or whatever is acting as the robot ‘hand’. However, it is worth double checking that the maximum payload does include this weight. To be certain the robot will be capable of lifting the desired weight, ask for the maximum payload with and without the proprietary EOAT.
At this stage, you should also consider whether you may change the EOAT in the future. For instance, if you plan to use the robot for several applications, you will need to change to a different gripper. Naturally, changing the EOAT will change the weight of the arm and therefore change the maximum payload of the robot.
Moment of inertia
By definition, inertia describes where an object resists changes in velocity. From a robotics perspective, inertia is a calculation that must be done before a robot is purchased.
Determining payload requirements is straightforward – calculate the weight the robot needs to lift. What isn’t obvious is that a robot will have limits on how fast it can move with certain weight, and in which directions. For example, a 6-axis robot may be able to lift 20kg, but this does not mean it can move 20kg quickly. Let’s face it, if the robot it cannot perform this movement at high speeds, or in the correct directions, it is a wasted investment.
Determining inertia requires multiple calculations. This includes collecting data for the total mass of the load, the shape of the load and how the load mass is distributed over the load itself. Put simply, exactly what the robot needs to lift and in what direction.
Most reputable robot suppliers will assist you in confirming whether a robot can actually deliver what you need based on inertia calculations, but it is worth assessing these measurements yourself, before approaching a supplier.
Robot installations are on the rise. If you are considering investing in a robot, be sure to consider these three calculations before parting with your cash. For more advice, speak to the team at TM Robotics at info@tmrobotics.com.